
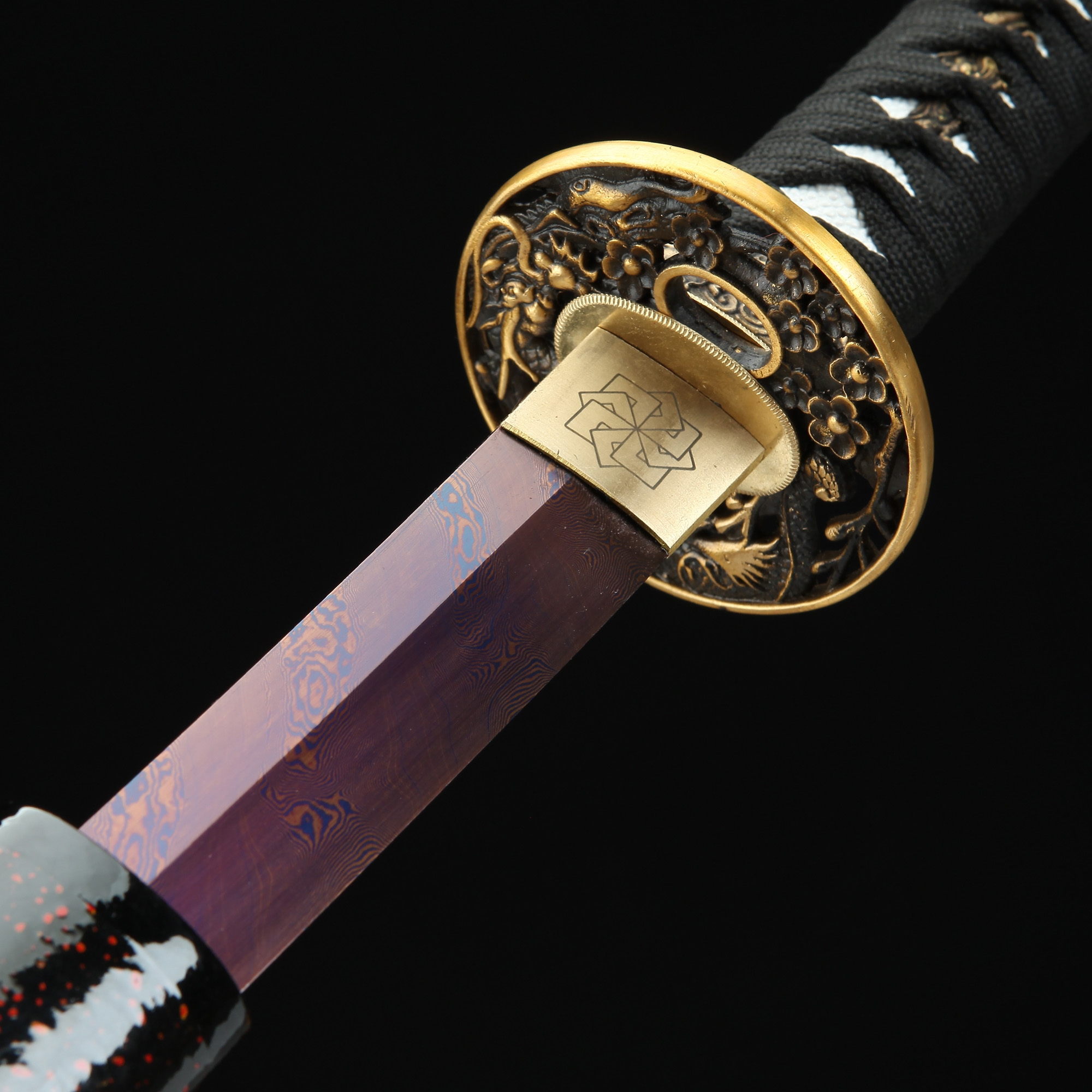
These final steps produce finishing touches that are as much a work of art as the blade itself. The handle is then fashioned with gold, leather and/or stone. Carpenters then fit the blade with a lacquered wooden scabbard, which artisans then intricately decorated. Metalworkers mount the blade with its decorative guard (at the sword's hilt). This polishing step can take several weeks, sometimes months.
#Real katana series#
The blade is meticulously polished with a series of grinding and polishing stones to hone the sword’s razor edge. Now fully forged, the blade is passed to the sword polisher. This process gives the sword its signature curve. The difference in the degree and speed of contraction between the two forms of steel in the blade causes the sword to bend. The blade is pulled from the fire and plunged or ‘quenched’ into water. Any hotter and the blade is at risk of cracking. The blade is then fired to just below 815☌ (1500☏). This serves both to protect the blade and to give it its signature wavy design called the hamon, which is revealed later during the final polishing. A thick mixture of clay and charcoal powder is applied to the blade's upper sides and dull back edge, leaving the sword's primary edge only lightly coated. With the blade steel now ‘assembled’, it requires one last firing. Both types of tamahagane are now exactly where they need to be the hard steel forms the sword's outer shell to provide the sharp edge, while the tough, low-carbon steel serves as the durable core. The low-carbon steel is also heated and hammered into a strip that fits snuggly into the channel. The best pieces of tamahagane are sent to a swordsmith, who heats, hammers, and folds the steels repeatedly-up to 16 times- in order to further combine the iron and carbon, and to draw out any remaining impurities, or ‘slag’.Īfter the smith hammers all impurities from the different steels, high-carbon steel is heated and shaped into a long piece with a U-shaped channel. A sword composed of just one type of steel would result in a blade that would be too brittle or dull easily. When expertly combined, high-carbon steel and low-carbon steel will imbue the blade with a razor-sharp edge and toughness, respectively. From this, they break apart and separate the steel mass according to carbon content. This step is crucial, and requires the team to be on hand for 72 hours without pause.Īfter the three day smelting process is complete, the tatara masters break open the clay furnace to extract the tamahagane. Once the correct temperature is reached, it’s up to the tatara masters to carefully monitor the tatara, feeding in iron sand and charcoal as needed.

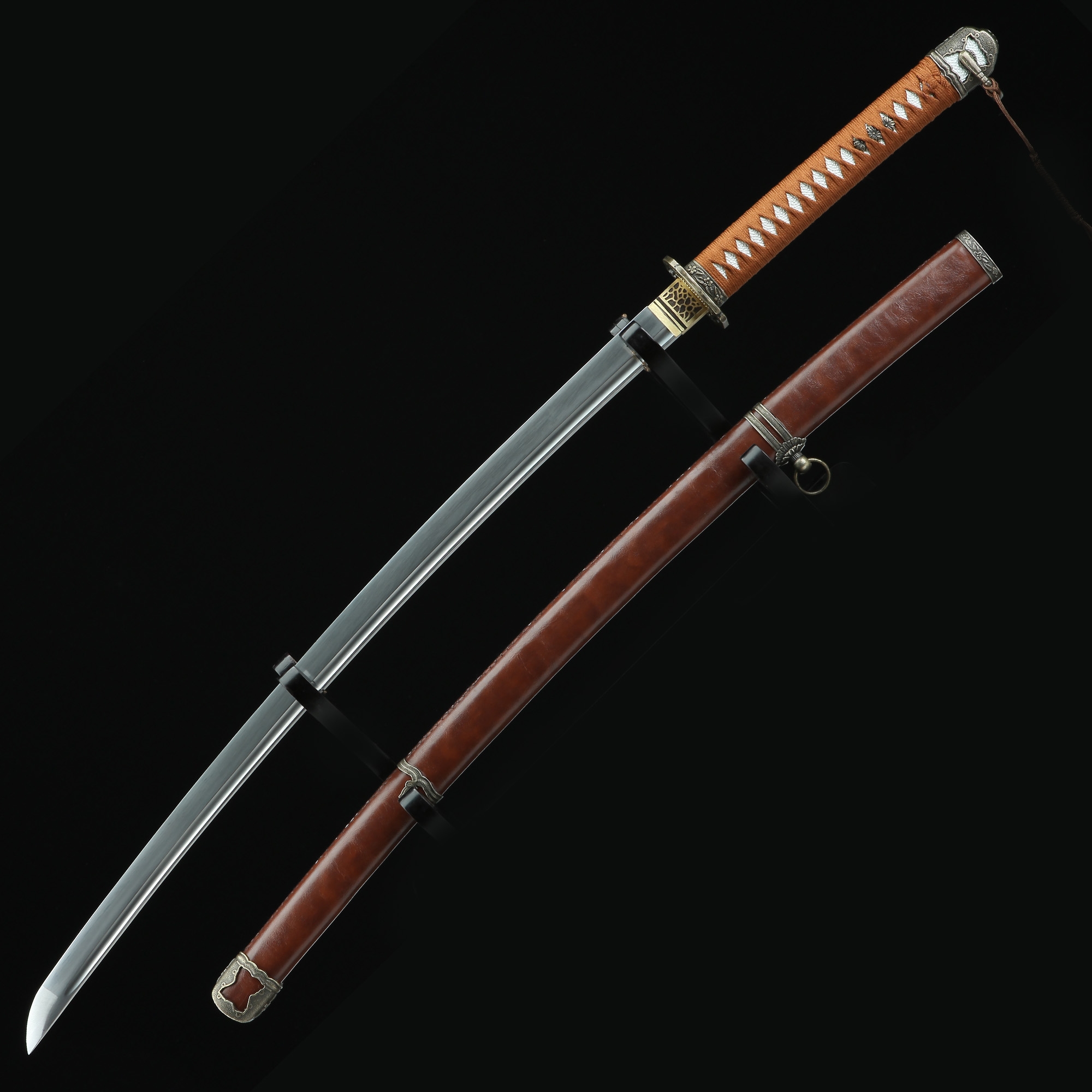
The starting steel, tamahagane, is produced by smelting iron sand (sand containing iron ore) with charcoal in a large clay furnace known as a tatara. Dozens of craftsmen would work around the clock for months on end, sometimes longer, to produce a single blade. Requiring a deeply intimate knowledge of chemical metallurgy, the traditional sword making process was anything but straightforward. The great swordsmiths of Japan were more alchemists than blacksmiths. Centuries ahead of its time, Japanese sword making was passed down from master to pupil for generations and revered as part art, part religious ritual. Said to possess a warrior’s very soul, the samurai sword has been marvelled at for its flawless beauty and unrivalled engineering for over a millennium. Of all the iconic national symbols, none is more representative of Japan’s time-forged traditions than the samurai sword.
